PVC shrink film is a popular choice for packaging, offering a blend of durability and versatility. This material is widely used across various industries due to its ability to tightly conform to the shape of the product, providing both protection and a professional appearance. This blog will walk you through the topic of PVC shrink films.
Understanding PVC Shrink Film
PVC shrink film, made from polyvinyl chloride, is widely used for packaging due to its durability and flexibility. It excels in creating a robust covering by contracting when heat is applied, making it suitable for various applications.
Properties and Advantages
PVC shrink film is known for its strong, flexible, and transparent nature. It provides a durable barrier that protects products from dust, moisture, and other external factors. The film’s ability to shrink tightly when exposed to heat, such as through a heat tunnel, ensures precise packaging.
Its reliable puncture resistance is a notable advantage, making it ideal for packaging items with sharp edges. Additionally, it’s cost-effective, accessible for non-food packaging, and provides a professional appearance.
Differences Between PVC and Other Shrink Films
PVC shrink film differs from other shrink films like polyolefin and polyethylene in several ways. Polyolefin shrink film, for example, is highly versatile and food-safe, often used as a replacement for PVC in food packaging. While PVC is a preferred choice for non-food items, polyolefin is known for its superior flexibility and clarity.
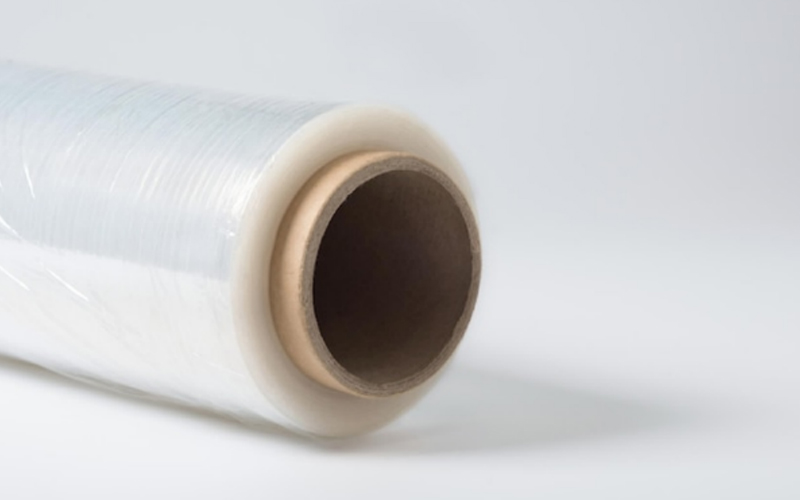
Comparatively, polyethylene lacks the transparency of PVC but offers a softer feel. PVC is valued for its balance of strength and affordability, marking distinct advantages over these alternatives. Centerfold PVC is a specific type that simplifies sealing by folding the film in half, providing convenience and efficiency in packaging applications.
Applications and Usage
PVC shrink film is a versatile material used for various packaging needs across different industries. It serves not only in basic wrapping tasks but also in more specific industrial applications.
Packaging Options and Formats
PVC shrink film offers multiple packaging formats such as tubing, single wound, and centerfold shrink film. These formats cater to distinct packaging needs, with centerfold PVC shrink wrap being commonly used due to its flexibility in size adjustments.
Tubing is ideal for products of diverse lengths. In contrast, single wound rolls suit applications requiring a continuous sheet. The film’s format is crucial, especially when used with a shrink wrap machine, as it influences the efficiency of automatic systems.
Industry-Specific Uses
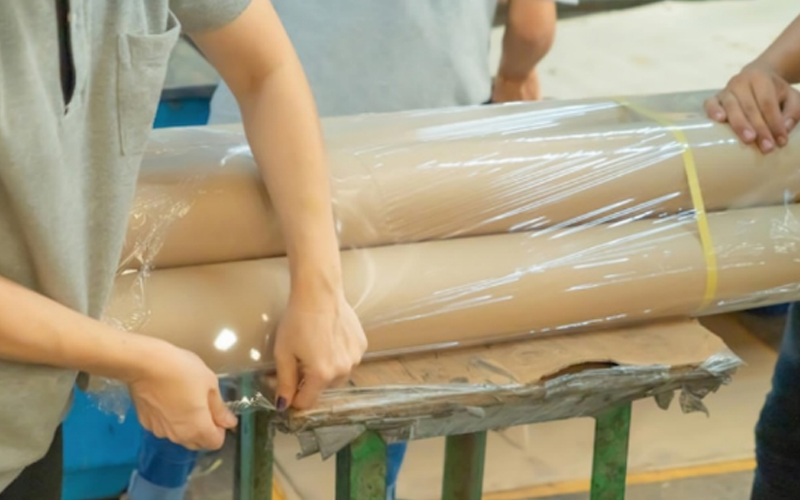
In the packaging industry, PVC shrink film is valued for its clarity and strength. It is frequently seen in retail settings, securing items like software and electronics.
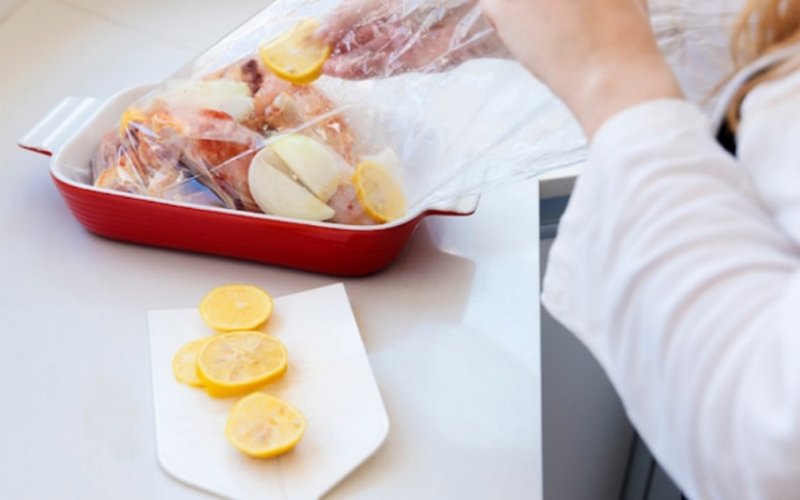
The film is also applied in direct food contact scenarios thanks to its protective qualities. Industries dealing with consumable goods often choose PVC shrink film for packaging materials needing durability. This is common in sectors that prioritize both the safety and presentation of their products.
Operational Considerations
Operational aspects of PVC shrink film involve critical decisions about selecting appropriate heat sources and addressing environmental and safety concerns. Each choice can impact the efficiency and safety of the packaging process.
Heat Source Selection and Settings
Choosing the right heat source is essential for optimizing the shrink process. Common options include heat guns and heat tunnels. Heat guns offer flexibility and are suitable for small-scale operations but require manual handling. Conversely, heat tunnels automate the process, enhancing speed and uniformity, ideal for high-volume production lines.
It’s important to note that PVC shrink film typically shrinks at lower temperatures compared to some alternatives. Adjusting heat settings accurately prevents issues like excess shrinkage or carbon deposits.
Maintaining the correct temperature ensures efficient energy usage and maximizes the value of the film as a packaging solution.
Environmental and Safety Concerns
Addressing environmental and safety concerns is crucial in PVC shrink film operations. Proper ventilation is vital when using heat sources, particularly in enclosed spaces, to dissipate any fumes produced during shrinkage. Implementing safety protocols minimizes employee exposure to potentially harmful emissions.
PVC film should be evaluated for its environmental impact as well. Although beneficial for packaging, users should explore sustainable options or eco-friendly practices to mitigate any adverse effects. Ensuring clear safety guidelines and regular monitoring further enhances a safe operational environment, while aligning with environmental standards and regulations.
Role of PVC Stabilizers
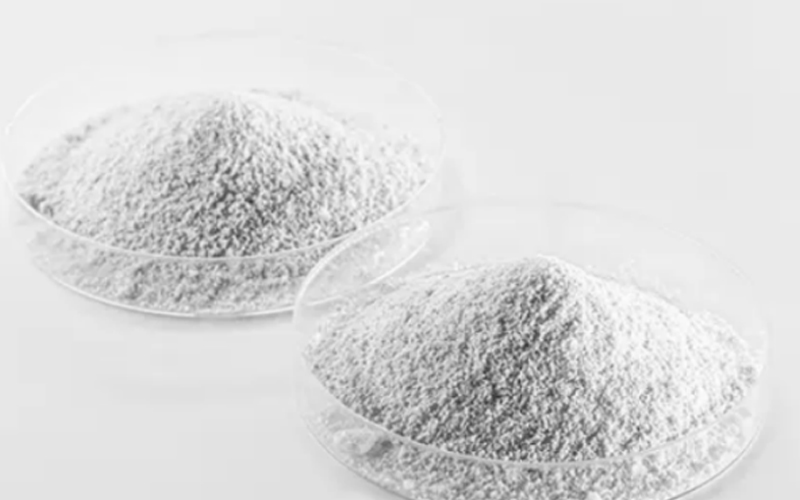
PVC stabilizers play a crucial role in enhancing the performance and lifespan of PVC products by preventing degradation and maintaining the material’s integrity. They are essential for maintaining the mechanical properties and appearance of PVC shrink film during processing and usage.
PVC Stabilizers
PVC stabilizers made by companies like Baisha prevent thermal degradation during processing by scavenging and neutralizing free radicals. This protection is vital, especially since PVC is thermally unstable at high temperatures. The use of stabilizers ensures that PVC products do not discolor or lose mechanical strength, which is critical for maintaining product quality and durability in applications like electrical cable insulation and PVC films. Metallic compounds like calcium-zinc and organotin are common stabilizer choices, each offering specific benefits.
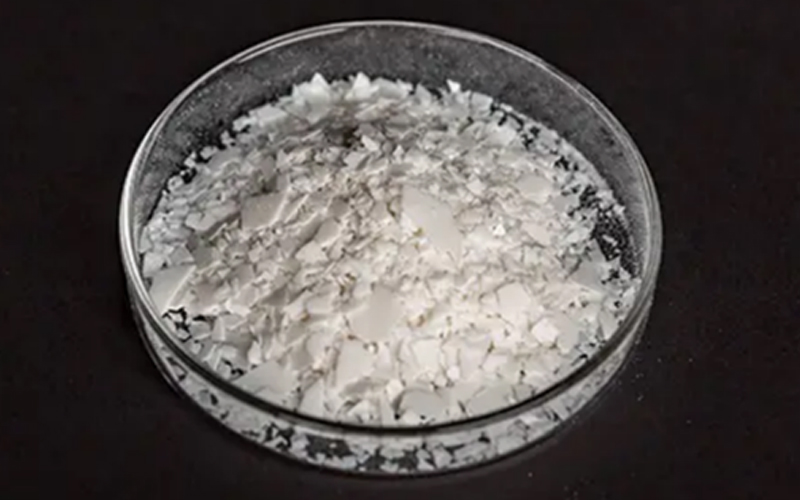
Stabilizers have a significant effect on the overall performance of PVC products, influencing properties such as flexibility and clarity. The type and quantity of stabilizer used can affect the shrink rate and mechanical properties of products like shrink film rolls, making them suitable for diverse applications.
Effect on PVC Shrink Film
In PVC shrink film, the role of stabilizers becomes even more critical. These films, available in various gauges like 100 gauge and 75 gauge, require stabilizers to ensure proper shrinkage performance during exposure to heat. Stabilizers help in maintaining shrink film integrity, contributing to the product’s flexibility and waterproof characteristics.
PVC shrink films are often used in colored shrink wrap applications where maintaining a consistent appearance during shrinkage is vital. Uline PVC film and similar products rely on stabilizers to retain color and clarity, ensuring that the end product remains visually appealing and technically sound.