Polyvinyl chloride, commonly known as PVC, is a versatile material used in various applications, from construction to clothing. Ensuring the thermal stability of PVC is crucial, as it is prone to degradation at high temperatures. This blog will navigate into the landscape of PVC stabilizers, providing essential tips on the top stabilizers for enhancing PVC materials’ performance and durability.
Fundamentals of PVC Stabilization
PVC, or polyvinyl chloride, is a versatile material widely used in numerous applications, from healthcare to construction. To maintain its properties and extend its lifespan, stabilizers are essential. This section will explore some crucial aspects of PVC stabilization.
Importance of Stabilizers in PVC
Stabilizers are crucial for preventing the degradation of PVC under various environmental conditions. They act by scavenging free radicals, thus maintaining the material’s color and mechanical properties. Without stabilizers, PVC would become brittle and discolored when exposed to heat or UV light. In healthcare applications, for instance, stabilizers ensure that medical devices remain safe and effective throughout their use.
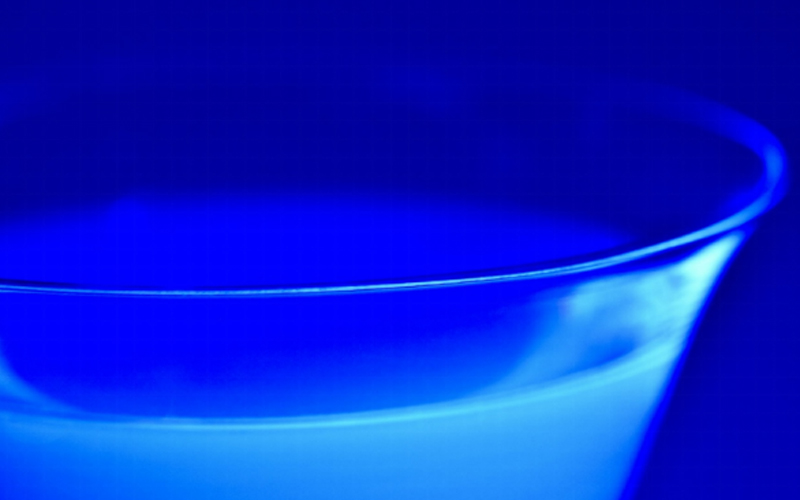
Types of PVC Stabilizers
There are several types of stabilizers used in PVC formulations, each with specific roles. Heat stabilizers protect against thermal degradation, which is a concern during processing. Common heat stabilizers include metal salts like calcium-zinc and organotin compounds. Light stabilizers and UV absorbers are essential for outdoor applications, shielding PVC products from UV radiation damage, which can lead to discoloration and embrittlement over time.
Mechanism of PVC Degradation
PVC degradation is primarily triggered by heat and UV exposure. Upon heating, PVC releases hydrochloric acid, which can further degrade the polymer chain. This leads to discoloration and a decrease in material properties. UV radiation also contributes to degradation by breaking chemical bonds. The inclusion of stabilizers slows down these processes by neutralizing free radicals and absorbing harmful radiation, preserving the integrity of PVC compounds.
Assessing Stabilizer Performance
Selecting an effective PVC stabilizer involves a careful examination of its impact on thermal stability, mechanical and electrical properties, as well as color stability and transparency. The right stabilizer can significantly enhance the performance and longevity of the product.
Evaluating Thermal Stability
Thermal stability is crucial for PVC as it is inherently sensitive to heat. A stabilizer’s ability to mitigate thermal degradation is central to its effectiveness. During processing, high temperatures can lead to discoloration and loss of mechanical integrity.
Effective stabilizers need to prevent this degradation by maintaining PVC’s stability up to its maximum operating temperature of 200°C (392°F). The stabilizer should be chosen based on the specific processing conditions and temperature requirements of the application.
Impact on Mechanical and Electrical Properties
Stabilizers affect not only thermal but also mechanical and electrical properties of PVC products. For mechanical properties, an ideal stabilizer increases material strength and flexibility. These effects are critical in applications where durability and resilience are needed.
Electrical properties are equally important in products such as cables. A stabilizer should enhance electrical insulation and stability. The performance characteristics of the stabilizer must align with the required mechanical and electrical standards of the end product, ensuring long-term reliability and performance.
Influence on Color Stability and Transparency
In PVC applications where aesthetics is paramount, the impact of stabilizers on color stability and transparency is significant. High-performance stabilizers should prevent yellowing and other color changes that can occur during processing and over time.
Transparency is crucial for applications like film and sheets. Stabilizers should be chosen for their ability to maintain clarity, as impurities or inadequate stabilization can lead to opacity. Selecting stabilizers with proven effectiveness in preserving color integrity and transparency enhances the visual appeal of PVC products and broadens their application scope.
Popular Stabilizers for PVC Applications
When selecting stabilizers for PVC, factors like heat resistance, application type, and environmental impact are essential. Common stabilizers are used across industries such as automotive, packaging, and construction, ensuring the durability of window profiles and fittings, among others.
Calcium Stearate and Zinc Stearate
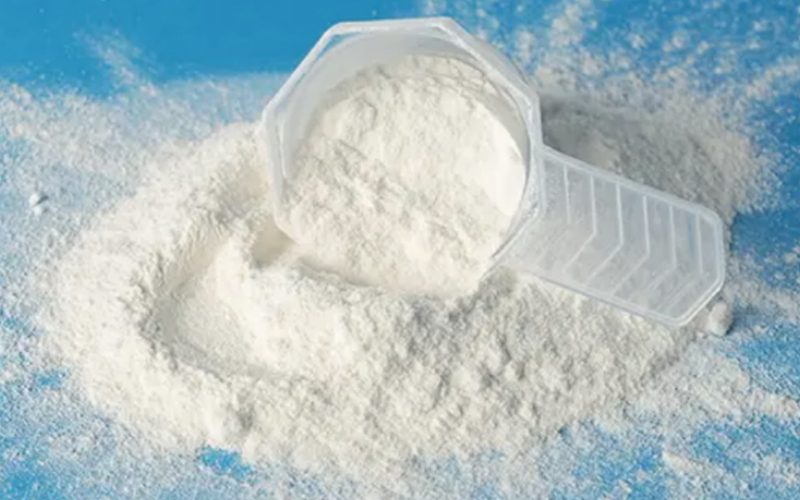
Calcium stearate and zinc stearate are well-regarded due to their low toxicity and effectiveness in various PVC applications. They function by scavenging acidic by-products formed during PVC processing. This increases the lifespan and mechanical properties of products like cables and automotive components.
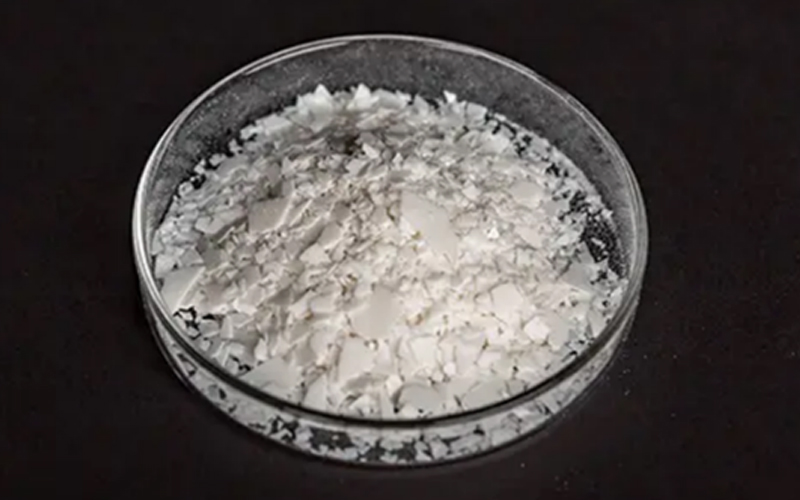
Calcium stearate is often used in rigid PVC applications, while zinc stearate finds widespread application in flexible PVC products. These compounds boast easy processing and improve the overall thermal stability of the material. They are frequently used in window profiles and other building materials, offering an environmentally friendly option for manufacturers.
Organotin Stabilizers
Organotin stabilizers are prominent in heat stabilization for PVC, used extensively in applications requiring high clarity and weather resistance, such as food packaging and medical devices. These stabilizers excel in rigid PVC formulations due to their superior long-term heat stability.
Their use in the automotive industry is also notable, providing durability for fittings and components exposed to varying temperatures. Moreover, their capability to enhance the physical properties of PVC makes them invaluable in specific applications.
Mixed Metals and Polyols
Mixed metals, which often include barium, cadmium, and lead, are combined with polyols to form stabilizers ideal for challenging PVC applications, such as in cables and pipes. Mixed metal stabilizers provide excellent heat stability and are suitable for both flexible and rigid PVC. They ensure superior mechanical strength in products that require longevity, making them suitable for packaging and industrial uses.
Polyols contribute additional thermal stability and lubricity. They act by inhibiting degradation reactions during processing. Utilizing high-purity compounds, these stabilizers deliver enhanced performance in complex applications while balancing environmental and regulatory considerations. Their versatility extends the functionality of PVC across a broad range of industries.
Sustainable Choices in PVC Stabilization
Sustainable stabilizers for PVC are gaining attention due to their reduced environmental impact. These alternatives often utilize non-toxic ingredients, improve product longevity, and support broader sustainability goals in various industries such as healthcare and food packaging.
Developments in Eco-Friendly Stabilizers
The shift towards eco-friendly stabilizers involves moving away from traditional lead-based compounds. Lead-free options, such as calcium zinc stabilizers, offer improved compatibility and longevity for PVC products. These stabilizers are especially beneficial in applications where human health is a concern, such as in healthcare and toys.
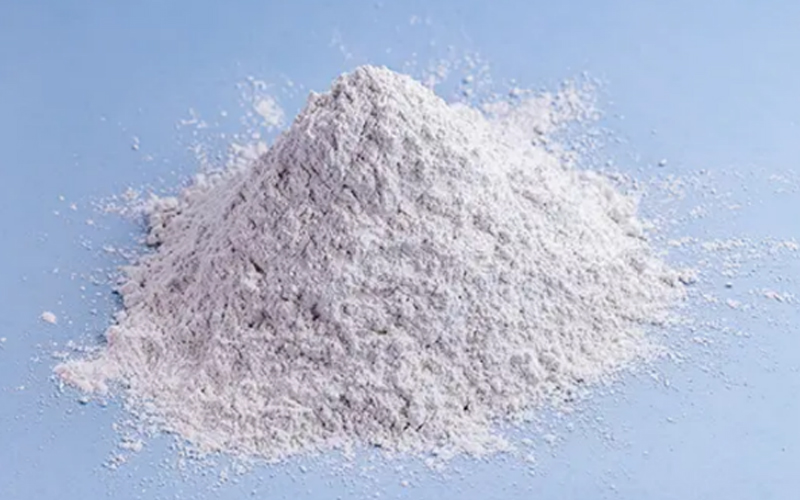
Enhanced formulations include antioxidants and UV absorbers, which help protect against degradation from sunlight, ensuring stability in outdoor applications like window profiles and irrigation systems. The use of these stabilizers can enhance the tensile strength and impact resistance of PVC materials, making them a reliable choice in sectors that demand durability.
Regulations and Market Trends
Increasing environmental regulations press manufacturers to adopt sustainable practices in PVC stabilization. Various regions enforce strict guidelines to minimize harmful substances in PVC products, driving market interest towards non-toxic stabilizers. The move to sustainable alternatives is not just regulatory, but also consumer-driven, with increased demand for safer, greener products.
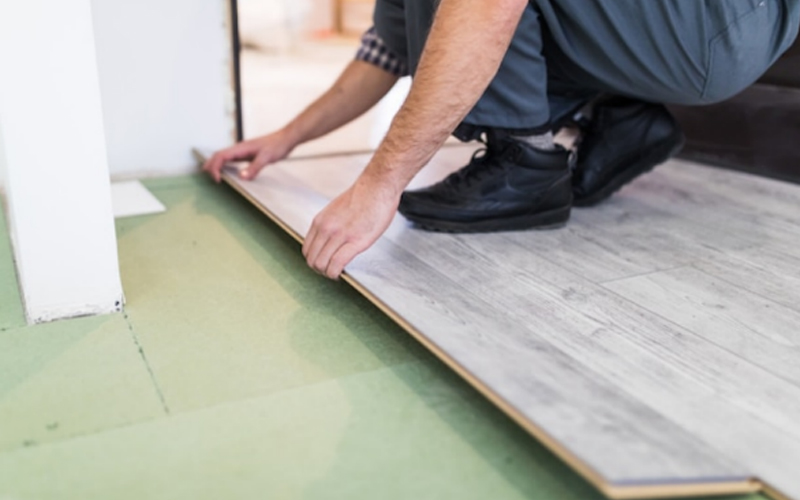
Moreover, market trends indicate a rising preference for stabilizers that aid in fusion and gelation processes, which enhance the efficiency of PVC production. As industries such as floor coverings and food packaging adopt these stabilizer solutions, they report significant benefits in product quality and compliance. This shift opens up opportunities for innovation in PVC heat stabilizers and S-PVC applications, aligning with global sustainability goals.