Polyvinyl Chloride, commonly known as PVC, is a versatile thermoplastic widely used in the construction industry and various industrial applications due to its durability and affordability. PVC pipes typically melt between 160°C (320°F) and 210°C (410°F), making it essential for users to be aware of its limitations in high-temperature environments.
Properties of PVC
Polyvinyl chloride (PVC) is a widely used synthetic polymer known for its diverse properties and versatility. It exhibits distinctive chemical, physical, mechanical, and thermal characteristics based on its formulation.
Chemical and Physical Properties
PVC is a thermoplastic polymer characterized by its chemical composition of repeating vinyl chloride units. The specific gravity of PVC is typically around 1.3 to 1.4, indicating it is denser than water. This material is available in rigid and flexible forms, with rigid PVC commonly used in construction for pipes and fittings due to its durability.
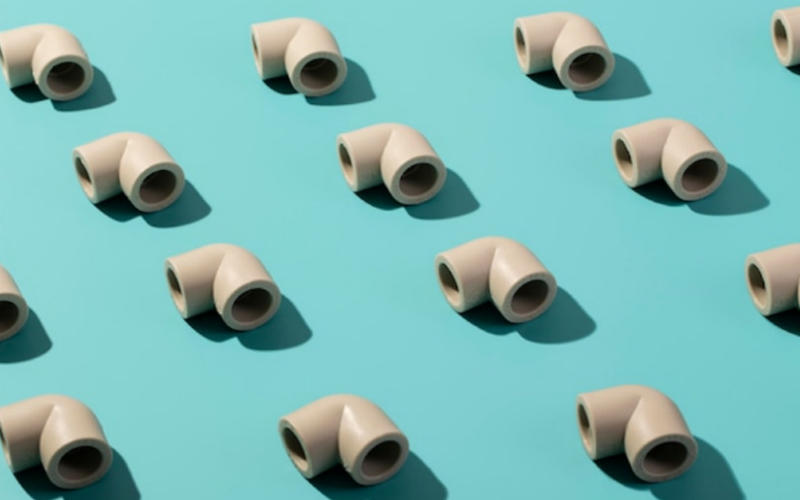
The molecular weight of PVC affects its mechanical properties. The PVC density influences its strength and flexibility, with higher densities often providing greater rigidity. PVC is inherently flame retardant, which adds to its appeal in building applications. Its flammability is low, but it can produce hydrogen chloride fumes when burned.
Mechanical and Thermal Properties
PVC’s mechanical properties include a tensile strength ranging from 2,000 to 6,000 psi in its rigid form. It has moderate hardness, making it an excellent choice for applications requiring impact resistance. Thermal properties of PVC dictate its suitability under heat stress. Its melting point is around 82°C to 260°C, dependent on formulation. This range allows for safe processing without degradation. The heat distortion temperature is significant as it defines the structural limitations under thermal load.
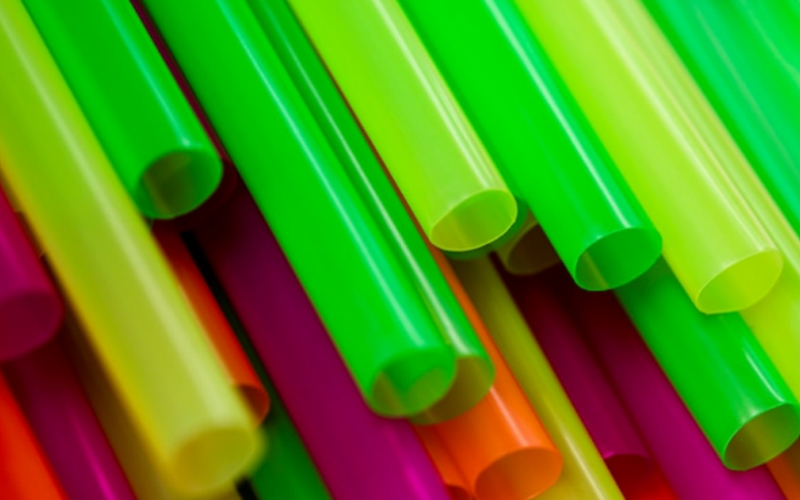
Thermal expansion is relatively low, making PVC ideal for construction materials that must remain stable with temperature fluctuations. PVC exhibits thermal stability, which means it resists rapid temperature changes, ensuring consistent performance in various environments. Overall, its heat resistance and robust mechanical profile make it a versatile choice across industries.
PVC Manufacturing and Formulation
PVC manufacturing involves precise processes to ensure the material meets desired specifications. The formulation significantly impacts characteristics like melting point, flexibility, and durability. Essential components such as plasticizers and stabilizers are added to achieve specific properties. Various processing techniques are employed to shape and solidify PVC for use in numerous industrial applications.
Compounding and Polymerization
In PVC production, compounding combines vinyl chloride monomer with plasticizers, stabilizers, and fillers. This mix is crucial for tailoring PVC properties. The process begins with the polymerization of vinyl chloride, forming PVC resin.
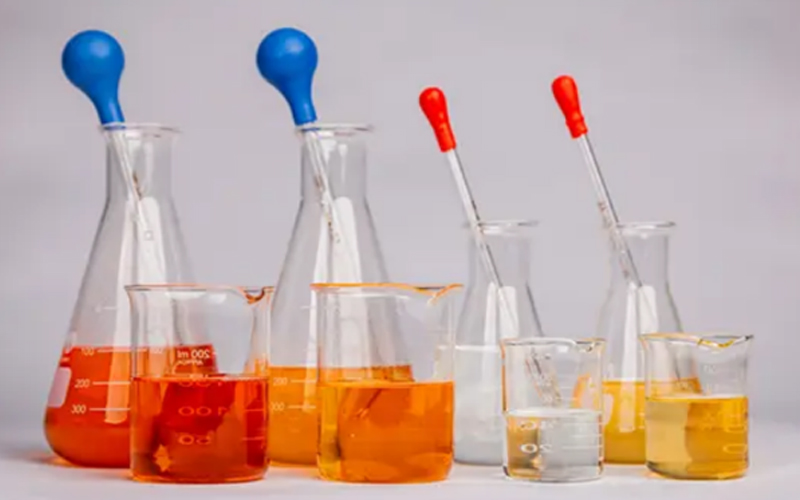
Plasticizers are added to increase flexibility, while stabilizers enhance heat resistance. Fillers can modify density and cost-effectiveness. Adjusting these additives can lead to variations in melting point and other properties, influencing the material’s performance in industrial applications like piping and roofing membranes.
Processing Techniques
The transformation of compounded PVC into usable products involves techniques such as extrusion and injection molding. In extrusion, the PVC mix is melted and pushed through a die, forming continuous shapes like pipes.
Conversely, injection molding injects molten PVC into a mold, creating detailed shapes such as fittings. Processing conditions are strictly controlled, with temperatures typically ranging from 170-210°C for melting and 20-60°C for molding. These techniques optimize the material’s properties for its intended function, whether in plumbing, sewage systems, or other applications where specific performance is critical.
Impact of Environmental Conditions on PVC
PVC pipes, being a thermoplastic material, are impacted by various environmental factors. High temperatures and direct sunlight are particularly influential in affecting the durability and structural integrity of these pipes.
Effects of Temperature and Sunlight
High temperatures can lead to softening and deforming of PVC pipes. Prolonged exposure to temperatures above the material’s melting range can cause structural changes, reducing the pipe’s ability to withstand pressure.
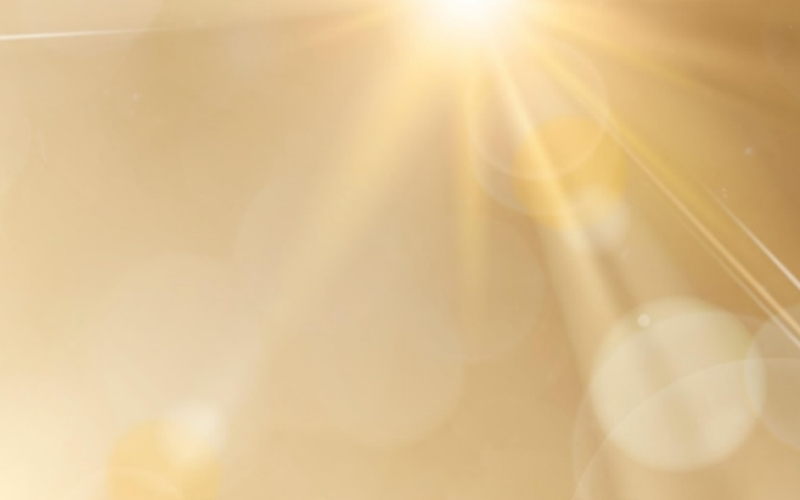
Direct sunlight is another factor that can damage PVC pipes. Ultraviolet rays in sunlight can lead to photodegradation. This process weakens the bonds in the polymer chains, causing embrittlement and fading. Over time, this can markedly reduce the lifespan of PVC in outdoor applications, like plumbing, unless the pipes are specially formulated with UV inhibitors.
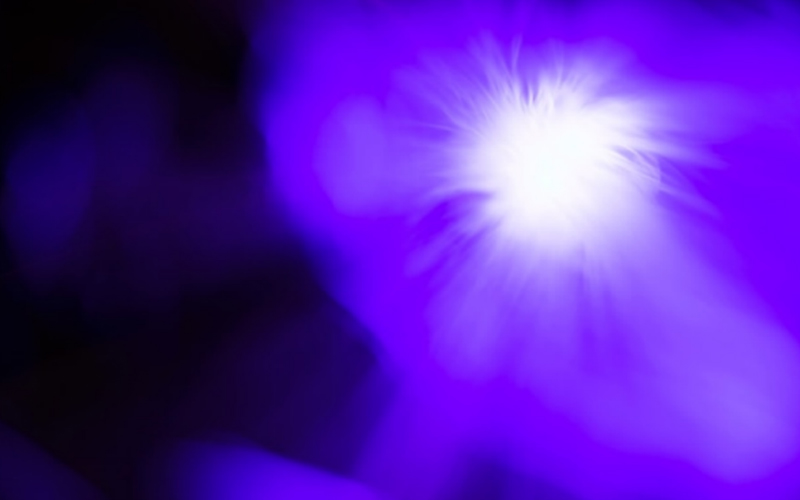
Longevity and Durability
Environmental conditions, such as humidity and fluctuating temperatures, contribute to the longevity and durability of PVC pipes. Constant exposure to harsh conditions without protective measures can lead to material fatigue. This can result in cracks or leaks.
PVC’s formulation can be adjusted for enhanced durability against environmental wear. Additives like plasticizers increase flexibility, while stabilizers improve heat resistance. Ensuring that PVC pipes are installed in environments with minimal harsh exposure and that the protection of these pipes is sufficient can extend their functional lifespan significantly.
Applications and Safety Standards
PVC pipes are widely used in various applications due to their versatility and safety standards. This section explores their industrial and construction uses, along with the necessary regulatory compliance and testing protocols.
Industrial and Construction Uses
PVC pipes are essential components in many industrial applications, including sewage, water distribution, and ventilation systems. Their high durability and resistance to chemical corrosion make them suitable for these demanding environments. Construction projects utilize PVC for plumbing systems due to its lightweight nature and ease of installation, which reduces labor costs.
Moreover, PVC’s Hazen-Williams factor contributes to its efficiency in fluid transportation by minimizing frictional losses. The material’s modulus of elasticity ensures reliable performance under pressure, making it ideal for both underground and above-ground installations.
Regulatory Compliance and Testing
Compliance with standards like ASTM D1784 is crucial to ensure the safety and reliability of PVC pipes. This standard outlines the material requirements for rigid PVC compounds used in pipes and fittings. Meeting these requirements ensures the materials’ suitability for various applications in construction and plumbing.
PVC pipes must also adhere to flammability ratings to prevent fire hazards. Testing protocols for these pipes involve assessments for pressure, temperature resistance, and environmental stress crack resistance. These tests guarantee that PVC piping can withstand the conditions of its intended use without significant degradation.