Polyvinyl Chloride, commonly known as PVC, is one of the most versatile plastics widely used across various industries. A significant concern in the production and application of PVC is its stability and resistance to degradation. This blog will walk you through the types and applications of PVC stabilizers vital to the stability of PVC materials.
Types of PVC Stabilizers
PVC stabilizers are essential for enhancing the durability and longevity of polyvinyl chloride (PVC) products. These stabilizers, including calcium-based, lead-based, tin-based, barium-zinc, and organotin stabilizers, each offer distinct advantages and applications in the industry.
Calcium-Based Stabilizers
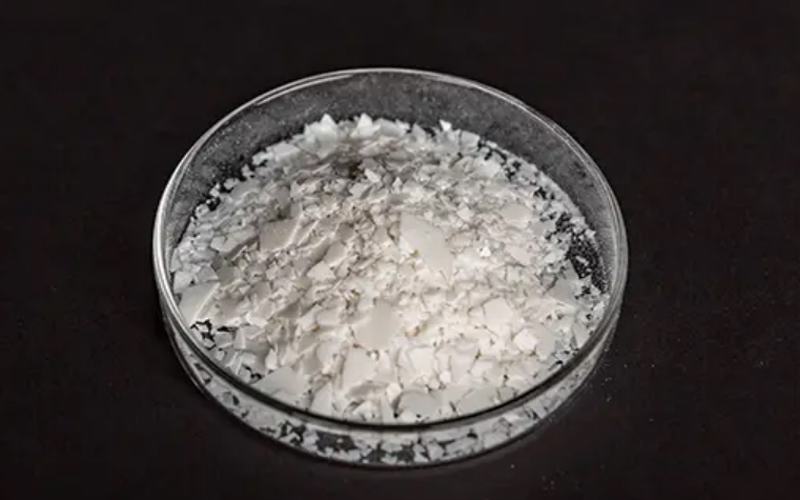
Calcium-based stabilizers are widely used in the PVC industry due to their low toxicity and environmental benefits. These stabilizers typically combine calcium with zinc or organic co-stabilizers, offering a balanced performance for both rigid and flexible PVC applications.
Calcium-zinc stabilizers excel in providing heat stability and weather resistance, making them suitable for outdoor applications such as pipes, window profiles, and cables. They are recognized for their transparency and resistance to sulfide staining, making them ideal for medical applications and food packaging.
Moreover, the non-toxic nature of calcium-based stabilizers ensures compliance with stringent environmental and health regulations, enhancing their appeal in sustainable manufacturing processes.
Lead-Based Stabilizers
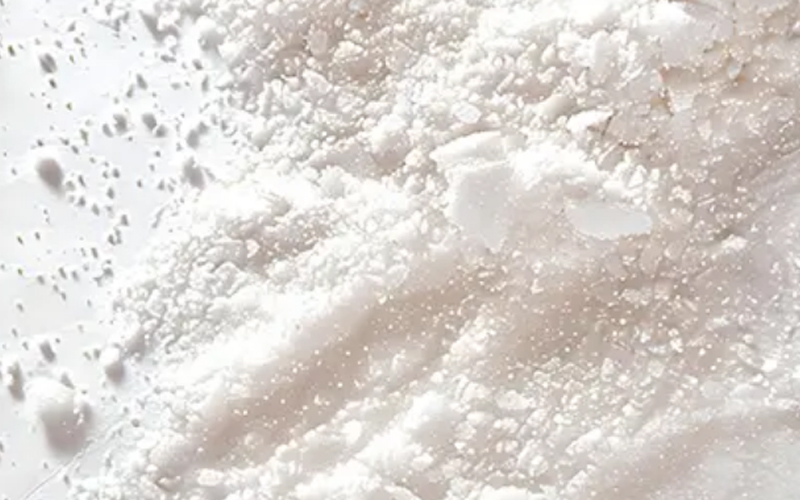
Lead-based stabilizers have been historically prominent in the PVC industry due to their effectiveness and cost-efficiency. These stabilizers provide excellent thermal stability, electrical insulation properties, and weather resistance, which are crucial for applications like cables, pipes, and profiles.
Despite their advantages, lead stabilizers are facing declining usage due to environmental and health concerns associated with lead exposure. Many countries have implemented stringent regulations to limit or ban the use of lead in PVC products, prompting manufacturers to seek alternative solutions.
Nevertheless, in regions with less stringent regulations, lead-based stabilizers remain in use due to their reliability and performance in demanding applications.
Barium-Zinc Stabilizers
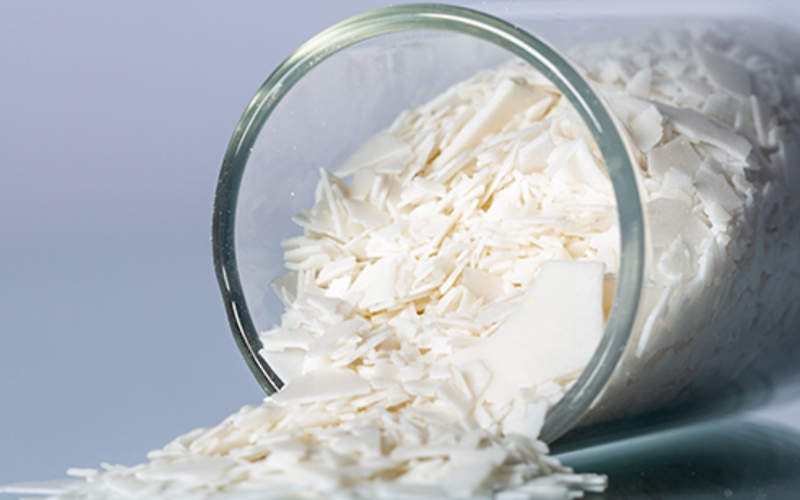
Barium-zinc (Ba-Zn) stabilizers provide a balanced solution for both rigid and flexible PVC applications, offering a combination of thermal stability and low toxicity. These stabilizers are particularly effective in preventing discoloration during processing and use, making them suitable for products requiring consistent appearance and performance.
Barium-zinc stabilizers are commonly used in applications such as automotive interior trims, flooring, and artificial leather. Their ability to maintain color and flexibility under various conditions makes them versatile stabilizers for a wide range of industrial uses.
Additionally, barium-zinc stabilizers are often favored for their cost-effectiveness and regulatory compliance compared to other metal-based stabilizers.
PVC Stabilizer Applications
PVC stabilizers are crucial for a variety of industrial and consumer applications. They ensure durability, enhance performance, and prevent degradation due to heat, UV exposure, and other environmental factors.
Construction Materials
PVC stabilizers are widely used in construction materials such as pipes, windows, and vinyl siding. For example, heat stabilizers protect PVC pipes from thermal degradation during the manufacturing process. UV stabilizers shield outdoor materials like vinyl siding from solar radiation, preventing discoloration and brittleness.
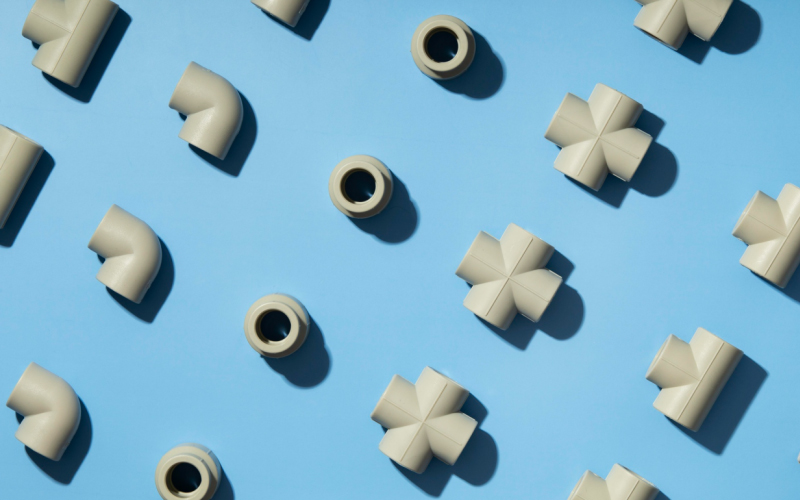
These stabilizers also enhance the mechanical strength of PVC products, making them suitable for heavy-duty applications such as sewer pipes and roofing membranes. This increases the lifespan of the materials, reducing maintenance costs and improving overall safety in construction projects.
Consumer Goods
In consumer goods, PVC stabilizers ensure products like toys, clothing, and packaging materials remain safe and durable. Calcium zinc stabilizers are commonly used because they are non-toxic and comply with health regulations, making them ideal for items that come into contact with children.
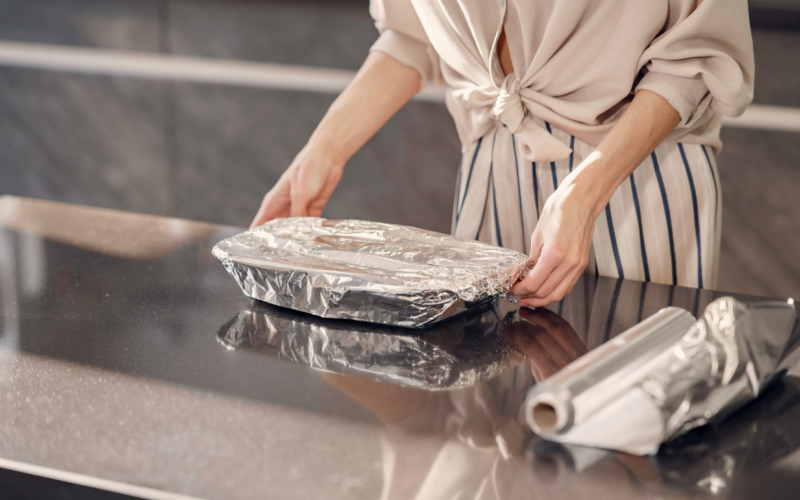
Mixed metal stabilizers, containing barium, cadmium, or lead, provide enhanced flexibility and are used in high-performance applications like synthetic leather clothing and flexible hoses. These stabilizers help maintain the integrity and appearance of consumer goods, ensuring they are both functional and aesthetically pleasing over time.
Role of PVC Stabilizers
PVC stabilizers play a crucial role in preventing degradation during processing and use. They also enhance performance, preserve color, and impact environmental sustainability.
Preventing Degradation
Stabilizers are vital in preventing the thermal and oxidative degradation of PVC. Without stabilizers, PVC material can degrade when exposed to heat and oxygen, leading to discoloration, brittleness, and loss of mechanical properties. These compounds work by neutralizing hydrochloric acid released during degradation, thus preventing further degradation reactions. Various types of stabilizers, including heat stabilizers and UV stabilizers, provide comprehensive protection across different conditions.
Enhancing Performance
PVC stabilizers enhance performance by improving mechanical strength, flexibility, and durability. Stabilizers enable PVC products to maintain their properties under stress, extending their lifespan and utility in various applications. For example, heat stabilizers allow for higher processing temperatures without compromising material integrity. This is particularly important in demanding applications like pipe manufacturing and electrical insulation, where material performance is critical for safety and functionality.
Color Preservation
One of the significant roles of PVC stabilizers is in color preservation. During thermal processing and exposure to light, PVC can undergo changes leading to discoloration. Stabilizers help maintain the material’s original appearance by scavenging free radicals and other reactive species that cause color changes. This is especially important for applications where aesthetics are important, such as in consumer goods and packaging.
Environmental Impact
PVC stabilizers also impact the environmental footprint of PVC products. Traditional stabilizers sometimes contain heavy metals, which raise concerns about toxicity and sustainability. Modern alternatives are being developed to address these issues. Calcium-zinc and organic-based stabilizers offer more environmentally friendly solutions, reducing harmful emissions and enhancing sustainability. These innovations contribute to the safer production and use of PVC, aligning with stricter environmental regulations and improving health and safety standards in the industry.