Polyvinyl chloride, commonly known as PVC, is a widely used plastic material found in numerous products ranging from pipes and cables to toys and medical devices. Its versatility is extended by its ability to be processed in various ways, including extrusion, molding, and calendaring. However, PVC inherently lacks thermal stability; during processing or over its lifespan, it can degrade when exposed to heat, leading to discoloration, loss of mechanical strength, and a decrease in performance.
To mitigate these risks and extend the longevity of PVC products, stabilizers are employed. They play a crucial role in preserving the material’s properties by neutralizing or scavenging free radicals generated during the processing phase or throughout the product’s use. These stabilizers come in different forms and compositions, suited to particular applications and manufacturing processes. They allow PVC to reach and maintain its desirable qualities such as clarity in packaging, flexibility in products like hoses and cables, and overall durability.
The category of heat stabilizers for PVC includes various compounds such as lead-based systems, calcium-zinc stabilizers, and organotin. Each type has its specific benefits and applications. Lead-based stabilizers, while highly effective in providing heat stability, are facing reduced usage due to environmental and health concerns, giving rise to alternative stabilizers like calcium zinc. These are notable for their non-toxic nature and suitability for a wide range of PVC applications, hence, they have become one of the most prevalent choices in the industry. Organotin stabilizers are often used for their efficient thermal stability and clarity, particularly in applications involving food-grade bottles and containers. It is through the proper selection and use of these stabilizers that PVC products meet the necessary standards of safety, performance, and durability.
Types of PVC Stabilizers

Reflecting a critical role in the longevity and quality of PVC products, PVC stabilizers enhance thermal stability and confer resistance against degradation during processing and usage.
Calcium-Based Stabilizers
Calcium-based stabilizers are now widely utilized as safe, non-toxic alternatives, particularly in PVC products designed for food contact or medical applications. Their primary function is to prevent discoloration and loss of mechanical properties at high temperatures.
Lead-Based Stabilizers
Lead-based stabilizers have historically been used for their excellent heat stabilization and durability. However, due to environmental and health concerns, their use is diminishing and being replaced by more eco-friendly options.
Tin-Based Stabilizers
Tin-based stabilizers are preferred in applications that demand high transparency and thermal stability, such as in the manufacturing of clear bottles and food packaging. They are effective in preventing degradation without the toxicity concerns associated with lead-based stabilizers.
Organic Stabilizers
Organic stabilizers, a category that includes a variety of chemical compounds, are used in PVC to cater to specific needs such as improved weather resistance or reduced volatility. They are suitable for applications where PVC will be exposed to harsh conditions.
Applications of PVC Stabilizers
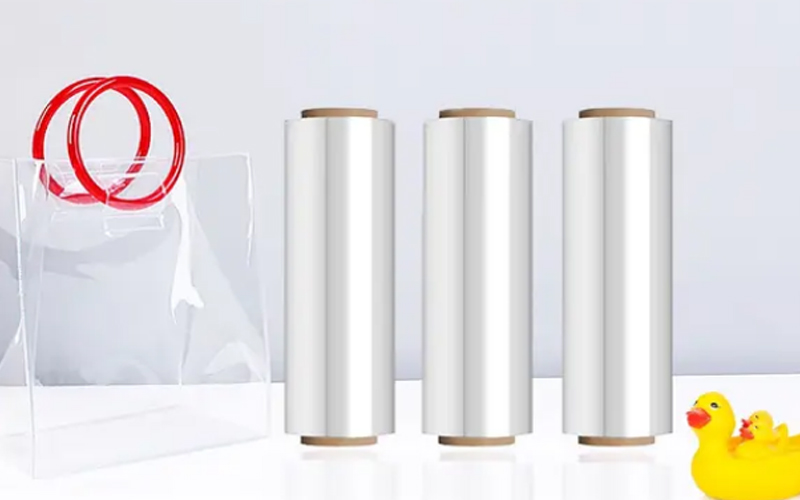
PVC stabilizers play a critical role in enhancing the performance and longevity of PVC products across various industries. By imparting heat stability and improving resistance to degradation, these additives extend the functional life of PVC applications.
PVC Pipes and Fittings
In the realm of plumbing, PVC pipes, and fittings represent a significant application sector for PVC stabilizers. They confer resistance to stresses and strains experienced under varying temperatures and pressures. The incorporation of stabilizers not only maintains the strength of PVC pipes but also prevents material decomposition during use.
Wire and Cable Insulation
For wire and cable insulation, PVC stabilizers are indispensable. These compounds permit PVC to withstand electrical, thermal, and mechanical challenges over time. Stability against heat is especially crucial to prevent insulation failure, which could lead to short circuits or electrical fires.
Window and Door Frames
Window and door frames made from PVC demand stabilizers for weather resistance and color fastness. These stabilizers protect the frames from ultraviolet light and thermal degradation, ensuring both functionality and aesthetic appeal remain intact over long periods.
Flooring and Wall Coverings
Lastly, flooring and wall coverings benefit significantly from the presence of PVC stabilizers. These are crucial for maintaining the material’s flexibility, allowing it to endure heavy foot traffic and resist wear and tear. The stabilizers also contribute to the longevity of the finish and texture of flooring and wall coverings.
Performance Characteristics
This section provides an overview of PVC stabilizers in terms of their contributions to enhancing the longevity and functional properties of PVC materials in various conditions.
Thermal Stability
PVC stabilizers play a crucial role in maintaining the polymer’s integrity when exposed to heat. Without proper stabilization, PVC degrades, leading to discoloration, loss of mechanical strength, and overall performance degradation. Stabilizers counteract these effects by neutralizing harmful free radicals formed during thermal processing.
UV Resistance
Exposure to UV light can cause detrimental effects on PVC, such as embrittlement and color changes. UV stabilizers are added to PVC formulations to absorb or block ultraviolet radiation, thus prolonging the material’s lifespan and appearance, particularly in outdoor applications.
Processing Stability
During the production and molding of PVC products, processing stabilizers ensure consistent material behavior. They facilitate smoother processing by preventing degradation and enabling the PVC to withstand the mechanical and thermal stresses of manufacturing processes.
Health and Environmental Impact
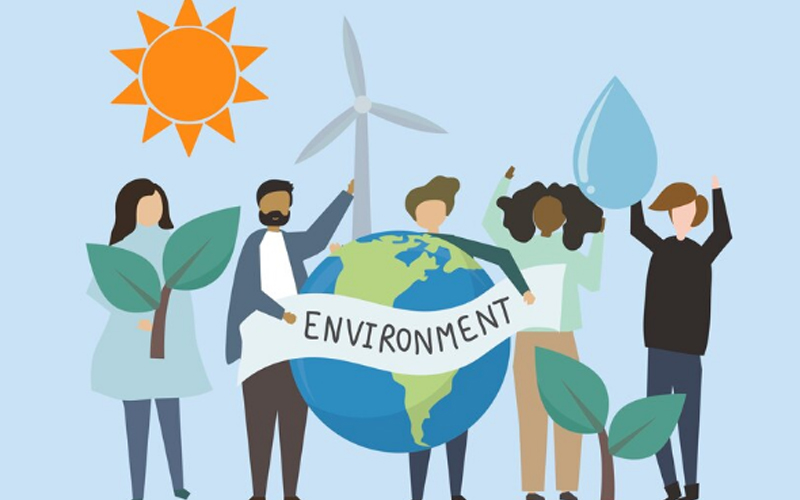
When considering the use of PVC stabilizers in manufacturing, it is crucial to understand the health and environmental concerns they raise. PVC production and stabilization can release harmful chemicals into the environment, posing risks to human health.
Regulatory Compliance
Regulatory agencies have set forth standards to mitigate the health and environmental risks associated with PVC stabilizers. In the European Union, the use of cadmium and lead-based stabilizers has been voluntarily phased out due to their toxicity. Alternative stabilizers that comply with regulatory demands include those based on calcium-zinc and barium-zinc systems, which are less harmful.
- EU Regulatory Action:
- Phased out: Cadmium (2001), Lead (2015)
- Current Systems: Calcium-zinc, Barium-zinc
Alternatives to Lead-Based Stabilizers
The shift away from lead-based stabilizers has led to the adoption of safer alternatives. These include organo-tin, barium, zinc, and calcium-based systems. Although these alternatives are considered less toxic, their environmental impact continues to be scrutinized to ensure safety and sustainability.
- Alternative Stabilizers:
- Organo-tin: Applied but under environmental scrutiny
- Barium and Zinc: Research indicates lower health risks
- Calcium-based: Emerging as a safe and effective option